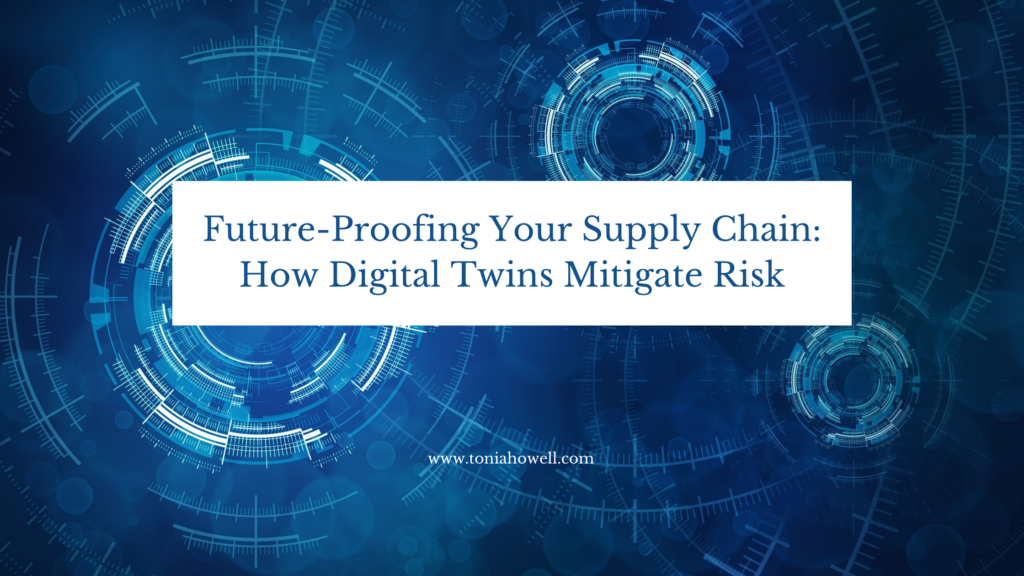
Written on spec
If we’ve learned nothing else over the last few years, we know being unprepared for the unexpected can affect our business. Supply chains can become fragile if not managed properly. As a result, businesses are now more apt to use technology to help mitigate risks. According to a recent survey, 86% of executives agree that their companies should invest more in technology to identify, track, and measure supply chain risks.
While the use of digital twin technology is often promoted in the manufacturing industry, supply chain professionals are realizing the benefits of using this tool in the scenario analysis process. In this article, we will explore the world of digital twins and how they can be used to help see future potential supply chain issues through scenario planning so you can anticipate supply chain issues and develop risk management strategies.
Identifying supply chain risks through scenario planning
A supply chain is simply defined as the movement of products or services from supplier to consumer. Anything that impedes the free flow of this process puts the supply chain at risk. Risks can be external such as natural disasters or internal such as off-the-mark forecasting and poor demand planning.
Scenario planning is a way for leaders to visualize how different risk factors or company decisions can affect the future of their business. Traditional scenario planning uses computer-aided design or CAD models for replication and are created based on set parameters for what could happen. These models are static and rely on new data to be fed into them to render new results.
Depending on the scenario, there are several different methods that can be used. Planning with the end in mind, companies will implement the normative scenario to represent how the business will operate once they’ve reached certain business goals. The quantitative scenario is used to plan out future financial forecasts providing models of both best and worst-case examples.
Operational scenarios are the most frequently used as they focus on the impact certain events can have on the business. Let’s take a look at how digital twins work and ways they can enhance the scenario planning process.
Understanding Digital Twins
A digital twin is a virtual representation of real-world entities and processes, synchronized at a specified frequency and fidelity. In contrast to CAD models, digital twins are created by pulling live data from several sources into one database. For physical products, this data transfer occurs through the use of IoT (Internet of Things) sensors. From here, the data is analyzed and fed into the digital twin. The digital twin uses this data to replicate the product, process, or system allowing businesses to examine what-if scenarios in real time and create solutions to mitigate those risks.
Similar to scenario planning, different twins are created based on what is being simulated. Product digital twins are implemented in the manufacturing sector and can be used to replicate large buildings or complex products. Businesses will use system digital twins to get an overview of how more intricate processes work together such as power grids and transportation networks.
Process digital twins are used across multiple business sectors including healthcare and retail. Also called process twinning, this method represents virtual replicas of workflows with the intent of finding bottlenecks in the process. This technique is applied to create supply chain digital twins commonly used to simulate warehousing and last mile logistics workflows.
When it comes to scenario planning, using digital twins over CAD models ensures you are receiving the most complete picture regarding potential supply chain risks.
Supply chain digital twins and risk scenario planning
Looking beyond workflow improvements, supply chain digital twins are the perfect tool for risk management. Here are a few scenarios where digital twin technology can help identify supply chain risks.
- Supplier Shut downs. There is plenty of economic uncertainty today. We’ve seen several businesses unable to weather the volatile environment and shut down due to bankruptcy. Internal labor disputes can cause companies to halt production. A lack of skilled workers can affect production levels as well. What would a disruption in product availability do to your supply chain as it operates today? Digital twins can use real time data to analyze this risk so you can develop a contingency plan and be ready to pivot when necessary.
- ESG Initiative implementation. ESG (Environmental, Social, and Governance) initiatives have become a high priority for businesses. More governments have mandated visibility into company ESG policies and performance. A poor ESG performance or lack of initiatives can put a company’s ability to obtain loans and investors at risk. Consumers are much more savvy and are making buying decisions based on whether they are aligned with a company’s values. According to a recent PwC article, 76% of consumers say they will stop buying from companies that treat the environment, employees or the community in which they operate poorly. Adopting these strategies can be huge undertakings for companies. By using digital twin technology, businesses can visually see how implementation can affect present day profitability and company goals for sustainability.
- Change in product mix. Pre-pandemic, supply chain leaders were comfortable using the just-in-time model to manage inventory. Needless to say, 2020 was a game changer. Everything from printers and ink to toilet paper and disinfectant wipes were flying off the shelves. Suppliers were not ready for this sudden shift in demand for these products. Today, many businesses have adopted a just-in-case model to avoid stock outs. Using a supply chain digital twin to simulate changing customer buying patterns in real time can help companies decide what products to have on hand and in what volume.
What you should know: Best practices for Implementing supply chain digital twins
So you’ve decided you’re ready to build your own supply chain digital twin to help with your scenario planning process, now what? Implementation requires a commitment of both time and money. Here are some things to consider when deciding how to integrate digital twins into your supply chain.
Know your risks
First, decide what risks you want to manage so you can plan for these scenarios. To prevent overwhelm, it’s a good idea to focus on the risks that provide the biggest ROI for your company if managed properly.
Know your data
Next comes the data gathering phase. Information should represent all supply chain processes and come from a number of sources. Having a large pool of relevant data for the twin to pull from will yield the most true to life outcomes.
Know your people
Ideally you will want subject matter experts and stakeholders from various areas of the supply chain involved in the development process. Digital twin creation is a large undertaking, and the more buy-in and collaboration you have from those involved the better.
Know your technology
According to a recent report, the digital twin industry is projected to grow to $73.5 billion by 2027. With this type of growth, more software options are coming on the market and can make choosing the right one challenging. While cost and ROI rank high when investing in new technology, these should not be the only things considered when deciding on digital twin software.
Easy data modeling, integration with current systems, and scalability to grow with your company are all important features to factor in during the evaluation process. Having a system that is easy to use can reduce time spent training staff and help accelerate deployment time.
Data security should also be top of mind. It should be clear how the digital twin can be accessed and how and where data will be stored. The platform should also allow for continued maintenance so data is kept current with the digital twins life span.
Final Thoughts
Mitigating as many supply chain risks as possible is important for business survival. Combining digital twin technology with scenario planning provides the best of both worlds by allowing businesses to see and compare what could happen with what is happening in real time. Armed with this data, businesses can create a plan of attack and be proactive in the face of potential risks resulting in a more agile supply chain. You can have peace of mind knowing you have a tool that gives you a virtual view of the impact certain risks could have on your supply chain. For more ways to improve the agility of your supply chain, click here.